The Role of Diecasting in Trendy Manufacturing
Diecasting is an essential manufacturing process that plays a substantial function in producing high-precision steel parts. This approach includes requiring molten steel right into a mold dental caries under high stress, developing complex and in-depth shapes with exceptional consistency and precision. Since its creation in the mid-19th century, diecasting has advanced with technological innovations, coming to be indispensable in sectors such as automotive, electronic devices, aerospace, and consumer goods. Its capacity to manufacture parts successfully and economically makes it a cornerstone of modern production.

The diecasting procedure begins with the design and manufacture of a die, commonly made from set steel, capable of standing up to the high stress and temperatures entailed. These dies are engineered to satisfy exact specifications, guaranteeing that the end product matches the intended design precisely. As soon as the die is ready, molten steel- usually light weight aluminum, zinc, magnesium, or copper- is infused into the mold and mildew dental caries at high stress. This pressure guarantees the liquified metal fills up every information of the mold, leading to a component that is highly precise and uniform. The rapid air conditioning and solidification of the steel within the die better boost the precision and surface area finish of the cast part.
Among the considerable advantages of diecasting is its capacity to generate get rid of excellent dimensional precision and smooth surface areas. This precision frequently gets rid of the demand for added machining and finishing procedures, reducing production time and prices. Diecast components are recognized for their stamina and durability, which makes them suitable for applications requiring high performance and reliability. The procedure likewise enables the unification of complicated functions, such as slim wall surfaces, ribs, and intricate geometries, which would certainly be difficult or difficult to achieve with other producing approaches.
Performance is another substantial advantage of diecasting, both in regards to material use and manufacturing rate. The process creates marginal waste, as any type of excess steel can be recycled and recycled in future casting operations. This efficiency not only makes diecasting an eco-friendly alternative but also helps reduce total manufacturing expenses. Furthermore, diecasting machines can generate a big volume of parts in a brief period, making them an excellent selection for automation. This high output is especially valuable in markets like vehicle production, where consistent top quality and quantity are vital. To receive supplementary details please look at Senadiecasting
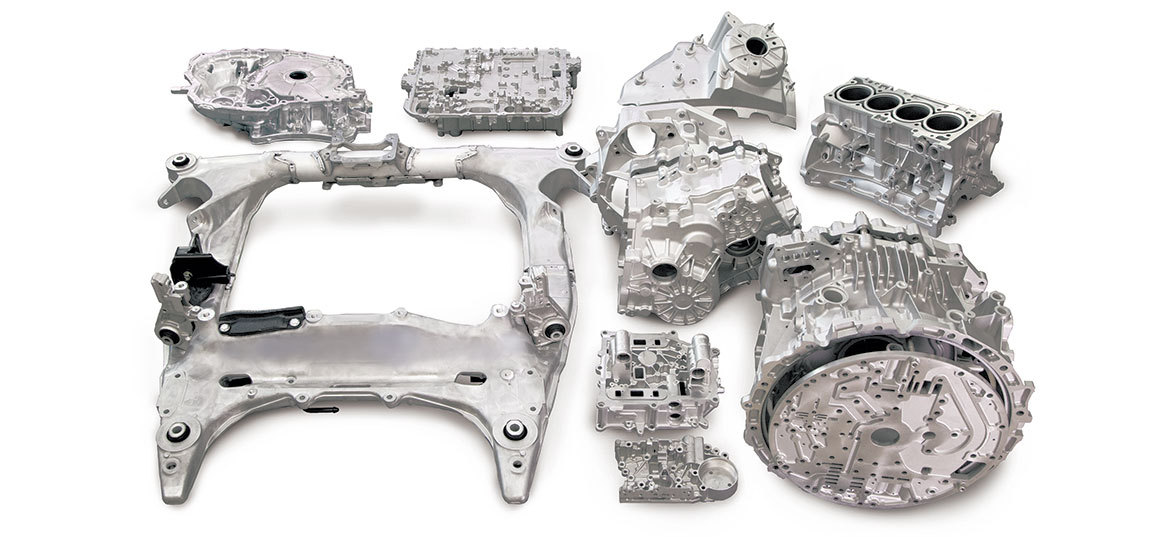
Regardless of its lots of advantages, diecasting does provide some obstacles. The initial price of developing the passes away can be substantial, making it a significant financial investment, specifically for small production runs. In addition, keeping precise control over the temperature and stress during the spreading procedure is vital to make certain regular quality, which can be technically demanding. Nevertheless, advances in diecasting innovation have dealt with many of these difficulties. Modern diecasting makers are outfitted with innovative control systems and real-time tracking capacities, enhancing process reliability and component high quality. These innovations have made diecasting extra available and effective, even for smaller producers.
Looking in advance, the future of diecasting is bright, with ongoing developments poised to further enhance the procedure and increase its applications. Developments in products science are bring about the development of new alloys that use premium mechanical homes and rust resistance. These innovative materials can boost the performance and longevity of diecast components sought after applications. Additionally, the integration of digital modern technologies, such as computer-aided style (CAD) and simulation software, is simplifying the die style and optimization procedure, lowering lead times and production expenses. As industries remain to look for high-quality, economical production solutions, diecasting is set to play a significantly vital role in satisfying these demands.